Industrial Applications
INDUSTRIAL APPLICATIONS
The bactericidal and cleansing properties of the Envirolyte solutions allow a wide range of industrial applications.
Food Industry
- Premises, processing equipment and work surfaces can be maintained at a high level of disinfection increasing efficiency.
- The Envirolyte solutions also enhance the shelf life of fruit and vegetables.
Office Cleaning
- Equipment and factory.
Ships, Planes and All Floating Vessels
- The quality of the contents of drinking water tanks can be maintained in a fresh state and the effects of leaching neutralised.
- Printing, paper, photographic and dyeing wastes
- Envirolyte solutions extractive qualities bleaches and cleanses wastes.
Breweries
- The needs of the breweries to clean/sterilise bottles and remove labels can be satisified by Envirolyte solutions which remove the need for use of chemicals.
Effluent Treatment
- Heavy metal industry is facing the problem of treating their highly contaminated effluents in the water. The huge oxidising, neutralising and flocculation properties of Envirolyte solutions offer the industry an effective way to treat these difficult effluents and to reduce dissolved harmful substances to a minimal level, not comparable to any existing alternative.
Cooling towers and Air Conditioners
- Envirolyte solutions are an efficient antidote to the main causes of problems in cooling systems, air conditioners and humidifiers. Bacterial pollution, scaling in pipes and pipe corrosion can all be avoided by application of these products.
- Envirolyte solutions prevent the growth of algae and aerobic bacteria such as legionella that cause corrosion of piping and equipment, fungi, foul odours and lime problems.
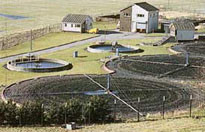
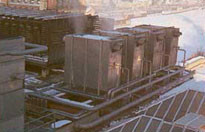
a - CIP OF THE PROCESSING EQUIPMENT IN VARIOUS INDUSTRIES
CIP WHICH IS NOW FASTER, CHEAPER AND ECO-FRIENDLY
Water processing with anolyte and catholyte or in other words Electrolyzed Water (EW) is used in a number of hygiene applications to remove unwanted microorganisms from contact surfaces in the food and beverage industry.
The multiple applications imply use anolyte for disinfection and catholyte as a washing fluid. Therefore there is a distinct need in the food processing, beer and beverage industries for the generators capable to produce both Anolyte and Catholyte.
Envirolyte CIP type of generators is ideally suited to these markets for CIP applications or hospitality markets (hotels, schools, government facilities, military bases, prisons, cruise ships, janitorial services, etc.). These generators are easy to install, operate and maintain and are the ideal solution when safety and cost are a concern.
Previously, beverage manufacturers would use traditional harmful chemicals to clean and sanitize to achieve similar results.
CIP is used during production when changing from one product to another or at specific times for hygiene reasons to eliminate the growth of harmful bacteria often present in water rich environments.
Traditional non-ECA chemical CIP steps are performed at high temperatures, and involve: a water rinse, followed by application of a detergent, followed by another water rinse, followed by application of a disinfectant, followed by a final water rinse, all of which require significantly more time, water and energy than cleaning with Envirolyte ECA solutions.
Replacing traditional chemical CIP with Envirolyte green ECA detergent and disinfectant solutions eliminates the need for high temperatures and eliminates the rinse between the detergent and the disinfectant steps reducing cleaning to a 4-step process, which results in a considerable reduction in the loss of valuable production time. This time saving cleaning process also saves energy and water for the bottler, resulting in greater profits and a greener CIP process.
The Envirolyte methodology helps beverage plants achieve sustainability goals, protect product & human life and improve profitability by providing, amongst others, the following benefits:
- Increased production time due to less time having to be spent on CIP;
- Total microbial decontamination;
- Reduction or complete elimination of costly and harmful chemicals;
- Savings on energy, with a reduction or elimination of the need to heat chemicals resulting in significant energy savings;
- Significant water savings;
- Flavour and residue elimination; and
- Improved safety for workers
In contrast to traditional chemicals, Envirolyte ECA Anolyte solution is produced and applied at a neutral pH, i.e. neither too acidic nor too alkaline, which makes it completely safe when in contact with humans and as an effluent in the environment. The ECA solutions can be used without any requirement for safety or protective gear.
The Envirolyte CIP range of anolyte/catholyte generators was developed in cooperation with our partners for the food processing and beverage market and is available in low salt configuration only.
b - OIL & GAS INDUSTRIES
Anolyte and Catholyte solutions have been used for stimulation and enhancement of oil and gas production and to improve performance of drilling fluids. Anolyte is a highly effective alternative to bactericides that are non-biodegradable or bio-accumulative. As a bactericide, Anolyte is selective, targeting bacteria responsible for microbial induced corrosion and slime while being safe to humans. Catholyte has been used to replace diesel oil as a cleaning solution for drill bits and tools on site.
Envirolyte anolyte solutions can be used to enhance production from wells which have been impacted by down-hole growth of bacteria, and other micro-organisms, by killing the bacteria and removing the restrictive biomass.
Water used for the fracturing of oil and gas wells can be treated with anolyte solutions to manage bacteria, protecting fracturing fluids and gels, and ensuring polymer and improved performance. Anolyte solutions remove scale and slime build-up from pipes, and cooling water systems can be kept free of biomass, improving heat exchange values and eliminating corrosion caused microbial induced corrosion (MIC). Produced water may be treated before being revised in stimulation fluids or water floods.
Recent data collected from field operations where frac water was treated with anolyte, shows that the bacteria levels in the frac water were reduced below the threshold level that would adversely impact stimulation fluids and gels.
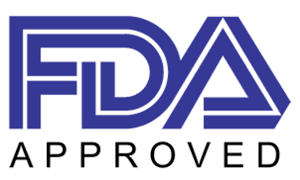
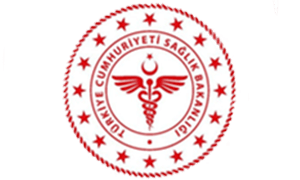
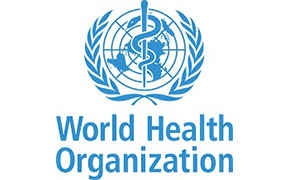
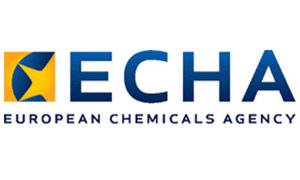
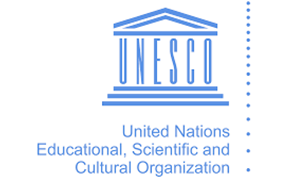
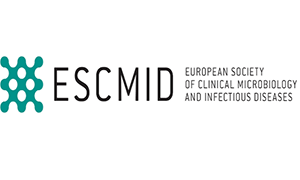
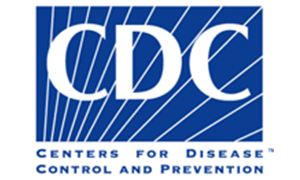

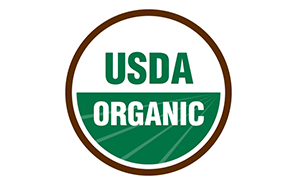
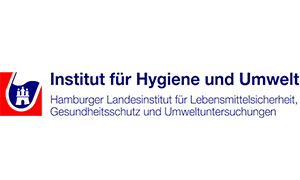